The global market for pyrolysis plants is expanding rapidly, driven by increasing demand for sustainable waste-to-energy technologies. Urbanization and industrialization generate substantial quantities of plastic, rubber, and biomass waste, creating opportunities for energy recovery through pyrolysis. Investors are recognizing the strategic advantage of integrating pyrolysis into circular economy models, where waste is transformed into fuel, oil, and char. Pyrolysis machine cost remains a critical consideration, with advanced systems offering higher efficiency and lower operational expenditure over time.
Beston - Recycling for Better Life!
Tuesday, August 19, 2025
Friday, August 8, 2025
The Use of Pyrolysis-Derived Oil as an Alternative Industrial Fuel
Pyrolysis-derived oil, often referred to as bio-oil or synthetic fuel oil, is gaining prominence as an alternative to conventional fossil-based industrial fuels. Produced through the thermal decomposition of organic or polymeric feedstocks in an oxygen-deficient environment, this liquid fuel offers a pathway to convert waste streams into a usable energy carrier. Its adoption addresses both resource scarcity and waste management challenges, particularly in sectors with high thermal energy demand.
Production Process
The generation of pyrolysis oil begins with feedstock preparation, where materials such as biomass, scrap rubber, or post-consumer plastics are size-reduced and dried. In systems like a plastic into fuel machine, controlled pyrolysis occurs within a sealed reactor at temperatures typically between 350°C and 500°C. Under these conditions, long-chain molecules are cleaved into shorter hydrocarbons, which condense into a liquid fraction upon cooling.
By adjusting thermal profiles, residence times, and catalyst inputs, operators can influence the viscosity, calorific value, and chemical composition of the resulting oil. The process also yields combustible gases and char, both of which can be used internally to sustain reactor heat balance, enhancing overall energy efficiency.
Industrial Applications
Pyrolysis-derived oil is utilized across a range of energy-intensive industries. In cement kilns, it serves as a partial or complete substitute for heavy fuel oil, providing high flame temperatures and stable combustion characteristics. Metal smelting operations use it as an auxiliary heat source, while brick and ceramic manufacturing benefit from its ability to deliver consistent thermal profiles.
Certain marine and stationary engines can operate on refined pyrolysis oil after minimal modification, offering a renewable alternative to diesel. Additionally, the oil’s adaptability makes it suitable for direct firing in industrial boilers, particularly in facilities equipped to handle variable fuel properties.
Environmental and Economic Benefits
Substituting conventional petroleum fuels with pyrolysis oil reduces dependence on imported crude and mitigates exposure to price volatility. From an environmental perspective, this transition curtails net greenhouse gas emissions, especially when the feedstock is waste-derived. Diverting plastics, biomass residues, or used tires from landfill or open burning not only reduces environmental contamination but also transforms these materials into valuable energy resources.
For facilities located near abundant feedstock sources, integrating a pyrolysis system reduces transportation costs and ensures a steady fuel supply. The closed-loop potential—where process by-products help sustain reactor operations—further improves economic feasibility.
Challenges and Optimization
Despite its advantages, pyrolysis oil presents certain operational considerations. Its higher oxygen content compared to petroleum fuels can lead to increased acidity and lower storage stability. Pre-treatment or upgrading methods, such as hydrodeoxygenation or blending with conventional fuels, are often employed to meet industry-specific performance criteria.
Ongoing advances in reactor design and catalyst formulation continue to enhance yield quality and consistency. Modern plastic into fuel machine configurations incorporate automated feed systems, advanced condensation units, and integrated emission controls, aligning with regulatory requirements and industrial reliability standards.
Conclusion
Pyrolysis-derived oil stands as a viable alternative fuel for industrial applications, merging waste valorization with energy production. When produced and managed effectively, it offers a renewable, locally sourced, and economically resilient option for sectors seeking to reduce carbon intensity while maintaining operational performance.
Thursday, July 17, 2025
The Positive Impacts of Thermal Desorption Pyrolysis on Oil Sludge Treatment
Oil sludge is a significant environmental concern, particularly in industries like petrochemicals, oil refining, and offshore drilling. Consisting of a mix of oil, water, heavy metals, and solid waste, oil sludge is notoriously difficult to treat and dispose of safely. As conventional waste management methods often fail to meet environmental standards, thermal desorption pyrolysis has emerged as an effective and eco-friendly solution for treating these contaminants. In this blog post, we’ll explore the positive role that thermal desorption pyrolysis plays in addressing oil sludge contamination, its benefits, and the challenges it can help overcome.
What is Thermal Desorption Pyrolysis?
Thermal desorption pyrolysis is a waste treatment technology that uses heat to break down organic pollutants in contaminated materials like oil sludge. The process involves heating the sludge in a controlled, oxygen-free environment to a temperature high enough to vaporize the hydrocarbons, separating them from solid residues. These hydrocarbons can then be condensed into liquid or gas form, leaving behind purified solid material (typically in the form of carbon or char).
Pyrolysis is particularly effective for treating materials with high levels of complex organic pollutants because it decomposes them into smaller, less toxic molecules. This makes thermal desorption pyrolysis a valuable technology for dealing with oil sludge, which often contains toxic chemicals, heavy metals, and hydrocarbons that are challenging to remove using traditional methods.
How Thermal Desorption Pyrolysis Works on Oil Sludge
Oil sludge is generally made up of a mixture of hydrocarbons, water, solids, and contaminants like sulfur, nitrogen compounds, and heavy metals. The treatment of oil sludge via thermal desorption pyrolysis typically occurs in three stages:
-
Heating: The sludge is heated in a reactor to temperatures between 300°C and 800°C in an oxygen-deficient environment. This step helps break down the complex organic compounds in the sludge, turning them into vaporized hydrocarbons.
-
Desorption: During the heating phase, volatile compounds (such as oil and gases) are driven off from the sludge. These compounds are then captured and condensed into useful products like oil or gas, which can be further refined or used as energy sources.
-
Char Residue: The remaining solid material, or char, consists of carbon, inorganic minerals, and residual contaminants. This solid byproduct can often be further treated or safely disposed of, depending on its composition.
The main advantage of this method is that it can treat a wide range of oil sludge types, even those with high levels of contaminants, and convert them into useful resources.
The Positive Impacts of Thermal Desorption Pyrolysis on Oil Sludge Treatment
Thermal desorption pyrolysis offers several environmental benefits when it comes to dealing with oil sludge. Here are some of the most notable positive impacts:
1. Effective Removal of Toxic Pollutants
Oil sludge contains various harmful contaminants, including heavy metals (like lead, mercury, and arsenic), sulfur, nitrogen compounds, and hydrocarbons. Traditional methods of treating oil sludge, such as landfilling or incineration, often fail to completely remove these pollutants, which can lead to soil, air, and water contamination.
Thermal desorption pyrolysis effectively breaks down many of these harmful substances. The high temperatures and oxygen-free environment prevent the formation of toxic byproducts, allowing for the efficient removal of organic contaminants. In addition, the separation of toxic heavy metals into the solid residue allows them to be dealt with more easily and safely.
2. Resource Recovery and Energy Generation
One of the key benefits of thermal desorption pyrolysis is its ability to convert oil sludge into valuable products. The hydrocarbons released during the process can be condensed into oil or gas, which can be used as an energy source. This can help offset the costs of the treatment process, making it economically attractive.
For example, the liquid oil recovered can be further refined and used as industrial fuel or even converted into biofuel, while the gas produced can be used to fuel the pyrolysis process itself, making it more energy-efficient. The recovery of these resources not only reduces waste but also contributes to the circular economy by turning hazardous waste into usable products.
3. Reduced Environmental Impact
Thermal desorption pyrolysis offers a more environmentally friendly alternative to traditional oil sludge disposal methods, such as incineration and landfilling. Incineration often produces harmful air pollutants, including dioxins, furans, and particulate matter, which contribute to air pollution and climate change. Landfilling oil sludge can lead to the leaching of contaminants into the soil and groundwater, potentially causing long-term environmental damage.
In contrast, thermal desorption pyrolysis takes place in a closed, controlled system, minimizing the release of harmful emissions. The process is designed to capture volatile organic compounds (VOCs) and other gases, preventing them from escaping into the atmosphere. The char byproduct can also be safely handled or used for further applications, ensuring minimal environmental impact.
4. Improved Waste Management Efficiency
Thermal desorption unit is a relatively efficient method for treating large volumes of oil sludge, which is crucial in industries like oil refining and offshore drilling. The ability to treat a wide variety of oil sludge types, including those with complex contaminants, makes it a versatile solution for many different sectors.
By converting waste materials into useful products, pyrolysis can significantly reduce the volume of oil sludge that needs to be disposed of. This helps mitigate the pressure on landfills and waste disposal systems, reducing the risk of environmental contamination and improving overall waste management efficiency.
5. Compliance with Environmental Regulations
With increasing global concern over environmental pollution, many regions have introduced stricter regulations regarding the disposal of hazardous waste, including oil sludge. Thermal desorption pyrolysis helps industries comply with these regulations by offering a cleaner, more sustainable method for treating contaminated materials.
By significantly reducing the hazardous nature of oil sludge, this technology helps companies meet the environmental standards set by local and international regulatory bodies, avoiding fines and improving their sustainability credentials.
Conclusion
Thermal desorption pyrolysis is proving to be a promising technology for treating oil sludge and its associated contaminants. By effectively breaking down hazardous materials, recovering valuable resources, and minimizing environmental impact, this process offers a cleaner, more sustainable alternative to traditional waste disposal methods. With ongoing advancements in pyrolysis technology, we can expect even greater efficiencies and broader applications, helping industries manage their waste more responsibly and contribute to a cleaner, healthier environment.
In the fight against pollution and waste, thermal desorption pyrolysis stands as an important tool in mitigating the environmental impact of oil sludge, moving us closer to a more sustainable future.
Wednesday, July 16, 2025
What Materials Are Pyrolysis Plants Recycling in Europe?
As the demand for sustainable waste management grows across Europe, pyrolysis plants have become an increasingly important part of the circular economy. These high-temperature systems break down waste materials in the absence of oxygen, converting them into valuable products like oil, gas, and carbon black. But what exactly are pyrolysis plants in Europe recycling?
1. End-of-Life Tires (ELTs)
One of the most common materials processed in European pyrolysis plants is used car and truck tires. These non-biodegradable rubber products are difficult to recycle through traditional methods. Pyrolysis allows for the extraction of:
-
Pyrolysis oil, which can be used as a fuel or chemical feedstock
-
Carbon black, reused in rubber and plastics manufacturing
-
Steel wires, often recovered and sold as scrap
Tire pyrolysis is particularly popular in countries like Germany, the Netherlands, and the UK, where strict landfill regulations encourage innovative recycling solutions.
2. Plastic Waste
With the EU pushing for plastic reduction and recycling targets, pyrolysis is seen as a way to handle non-recyclable or mixed plastic waste—especially polyethylene (PE), polypropylene (PP), and polystyrene (PS). These plastics are converted into:
-
Synthetic oil or naphtha, used in petrochemical production
-
Gases, which can be used to fuel the process itself
-
Solid residues, such as char
Countries like Spain, Italy, and France are investing in chemical recycling facilities to complement traditional mechanical recycling.
3. Biomass and Agricultural Waste
In some regions, especially Eastern Europe and Scandinavia, pyrolysis is used to convert agricultural residues, wood waste, or food processing byproducts into:
-
Biochar, a soil amendment with carbon sequestration benefits
-
Syngas, used for energy generation
-
Bio-oil, which can serve as a renewable fuel
This supports both renewable energy goals and rural waste management initiatives.
4. Sewage Sludge and Industrial Waste
In urban areas, some pyrolysis facilities process sewage sludge or hazardous industrial waste, reducing volume and eliminating pathogens while recovering energy. Although this use is less common, it is growing in countries with advanced waste-to-energy infrastructures.
Conclusion
Pyrolysis plants in Europe are playing a key role in recycling hard-to-process materials, especially tires and plastics. As technology advances and environmental regulations tighten, the scope of materials suitable for pyrolysis is expanding. This method not only reduces landfill use but also contributes to energy recovery and resource circularity—core values of Europe's green transition.
Sunday, June 29, 2025
Understanding the Costs of a Pyrolysis Plant: A Comprehensive Guide
As the world shifts towards more sustainable solutions for waste management and energy production, pyrolysis plants are gaining significant attention. Pyrolysis, the process of converting organic materials such as plastics, rubber, and biomass into valuable products like fuel, gas, and carbon black, is becoming an attractive alternative to traditional waste disposal methods. However, a common question arises for potential investors and businesses: How much does a pyrolysis plant cost?
What Affects the Cost of a Pyrolysis Plant?
The cost of a pyrolysis plant can vary greatly depending on several factors. Understanding these factors is crucial for anyone considering an investment in this technology.
1. Size and Capacity of the Plant
The scale of the pyrolysis plant is one of the most significant cost determinants. Pyrolysis plants come in various sizes, ranging from small units with a processing capacity of 5-10 tons per day, to large-scale plants capable of processing hundreds of tons of waste per day. Naturally, the larger the plant, the higher the cost.
2. Feedstock Type
The type of feedstock (the material to be processed) also influences the cost. For example, converting plastic waste or rubber might require more sophisticated technology and higher initial investment compared to biomass pyrolysis. The complexity of the feedstock and its processing requirements can raise or lower the overall cost of the pyrolysis plant.
3. Technology and Equipment
The pyrolysis machine cost itself plays a significant role. Some advanced pyrolysis technologies, such as high-temperature reactors, continuous feed systems, and multi-stage distillation systems, can increase the overall cost. Additionally, whether the plant uses a batch process or a continuous process will affect the cost, with continuous systems typically being more expensive but more efficient in the long run.
4. Location and Infrastructure
The location of the pyrolysis plant can significantly impact the total cost. In regions with high labor costs, stricter environmental regulations, or transportation challenges, the price tag for a pyrolysis plant can increase. Conversely, setting up a plant in a location with abundant feedstock availability and lower operational costs can reduce the overall cost.
5. Installation and Maintenance
The cost of installation and ongoing maintenance should not be overlooked. Installing a pyrolysis plant requires skilled labor, proper planning, and local regulatory approvals. Maintenance costs over the years can also add to the financial burden, as regular repairs, spare parts, and safety upgrades are necessary to ensure the system runs efficiently.
6. Permits and Regulatory Compliance
In many regions, the installation and operation of a pyrolysis plant require various permits and adherence to environmental regulations. Depending on local laws, this can add additional costs for certification, monitoring, and compliance with safety and environmental standards.
Operating Costs of a Pyrolysis Plant
Apart from the initial setup cost, running a pyrolysis plant incurs ongoing operating expenses, including:
-
Energy Costs: Pyrolysis is an energy-intensive process, and depending on the plant's design, it may require a significant amount of electricity or fuel to maintain optimal temperatures.
-
Labor: Staff wages and operational manpower are essential to keep the plant running smoothly.
-
Raw Materials: The cost of sourcing feedstock, if not sourced locally or in-house, can add to operational expenses.
-
Maintenance and Repairs: Regular maintenance to keep the machinery in working condition, along with spare parts and repairs, forms a part of the annual operational budget.
Potential Revenue and ROI
While the initial cost of setting up a pyrolysis plant can be significant, it’s important to keep in mind that these plants can be highly profitable over time. The revenues generated depend on the sale of the following products:
-
Pyrolysis Oil: Can be used as a substitute for diesel fuel in industrial applications.
-
Carbon Black: Used in rubber manufacturing, ink production, and as a fuel.
-
Syngas: Can be used to generate electricity or heat.
-
Charcoal: Can be sold for use in cooking, as a fuel for industries, or as a soil conditioner.
The return on investment (ROI) varies depending on market conditions, but many pyrolysis plant owners report positive cash flow within 2 to 5 years of operation, depending on the size of the plant and the local market for its by-products.
How to Minimize Pyrolysis Plant Costs
For those concerned with the cost of a pyrolysis plant, here are some tips to reduce overall expenses:
-
Start small: If you're new to pyrolysis, consider starting with a smaller plant to gain experience before scaling up.
-
Choose efficient technology: Investing in high-efficiency reactors and systems can reduce long-term operational costs.
-
Source feedstock locally: Reduce transportation costs by sourcing feedstock from nearby locations.
-
Invest in good maintenance: Proper care of equipment and regular maintenance can prevent costly repairs in the future.
Conclusion
The cost of a pyrolysis plant is influenced by multiple factors, ranging from size and capacity to feedstock type and location. While the initial investment can be significant, the long-term profitability of pyrolysis plants makes them an attractive option for sustainable waste management and energy production. By carefully considering all the variables involved, you can make a more informed decision about whether investing in a pyrolysis plant is right for your business.
Are you considering investing in a pyrolysis plant? What factors do you find most crucial in determining the cost?
Tuesday, June 24, 2025
How Can Pyrolysis Oil Be Upgraded?
Pyrolysis oil, also known as bio-oil, is a dark, viscous liquid produced by heating organic materials such as plastics, tires, or biomass in the absence of oxygen. This process, known as pyrolysis, breaks down the complex compounds in the feedstock into simpler molecules, resulting in liquid oil, gas, and solid residues like carbon black.
While pyrolysis oil can be used as a fuel itself—often in industrial burners or boilers—it has some limitations. It typically contains high levels of oxygenated compounds, water, and impurities that reduce its energy density and make it less suitable for high-performance engines or transportation fuels. However, upgrading pyrolysis oil to a higher quality can significantly increase its usability, value, and potential for large-scale commercial applications.
How Can Pyrolysis Oil Be Upgraded?
Upgrading pyrolysis oil involves removing impurities, improving its energy density, and refining its chemical structure to make it suitable for more advanced uses. Several techniques can be employed to upgrade pyrolysis oil into higher-quality fuels:
1. Hydroprocessing (Hydrotreating and Hydrocracking)
Hydroprocessing is one of the most common methods used to upgrade pyrolysis oil. It involves the addition of hydrogen to the oil under high pressure and temperature, which helps remove oxygen and other impurities like sulfur and nitrogen. The hydrogen treatment breaks down the larger molecules in the pyrolysis oil, producing lighter, more refined oils.
Hydrotreating: This process is used to reduce the oxygen content and improve the stability of the oil, making it more suitable for use as diesel or gasoline.
Hydrocracking: Hydrocracking breaks down heavier molecules into lighter fractions, further increasing the quality and making the upgraded oil usable in high-efficiency engines.
2. Catalytic Pyrolysis
In catalytic pyrolysis just like in a Beston plastic pyrolysis plant with catalytic dewaxing patent, a catalyst is used to break down large, complex molecules into smaller, lighter hydrocarbons. This process enhances the fuel quality by improving the oil’s energy content and reducing its viscosity. Catalytic cracking is a well-established technology used in the petroleum industry and can be applied to pyrolysis oil to produce high-quality fuels.
3. Distillation
Distillation is another method used to upgrade pyrolysis oil. In this process, the oil is heated and separated into different fractions based on their boiling points. This allows the extraction of higher-quality components, such as gasoline or diesel, by isolating the lighter fractions while leaving behind the heavier, less useful components. Distillation can help purify pyrolysis oil and improve its refined product yield.
4. Alcoholysis
Alcoholysis is a process in which pyrolysis oil is reacted with alcohols like methanol or ethanol to reduce its oxygen content. This process helps to convert some of the oxygenated compounds in the oil into higher-value fuel products. Alcoholysis can also be used in combination with other refining techniques to further enhance oil quality.
Benefits of Upgrading Pyrolysis Oil
Increased Fuel Efficiency: Upgrading pyrolysis oil to a higher-quality product increases its energy density, making it a more efficient fuel source. This is particularly important in applications where high-performance fuels are required, such as in transportation or power generation.
Broader Applications: High-quality pyrolysis oil, after upgrading, can be used in a wider variety of applications. It can be turned into transportation fuels, such as diesel or gasoline, or even be used in aviation fuel production, making it a more valuable and versatile product.
Reduced Environmental Impact: By converting low-grade pyrolysis oil into higher-quality fuels, the overall carbon footprint of the production process can be reduced. These upgraded fuels can be more easily integrated into existing infrastructure, helping to reduce the reliance on fossil fuels.
Economic Value: Upgrading pyrolysis oil opens up the opportunity to sell high-quality fuels at a premium price, increasing the economic viability of pyrolysis projects. This is especially valuable for businesses involved in waste-to-energy or circular economy initiatives.
Cleaner Burning: By removing impurities like sulfur, nitrogen, and oxygenated compounds, upgraded pyrolysis oil burns more cleanly, producing fewer harmful emissions. This contributes to better air quality and compliance with environmental regulations.
The Future of Pyrolysis Oil Upgrading
The market for waste-to-energy solutions is rapidly expanding as global plastic and waste management challenges grow. As more companies invest in pyrolysis technology, the demand for upgraded pyrolysis oil is expected to rise. Over the next few years, the focus will likely shift towards optimizing the upgrading process, making it more cost-effective, efficient, and scalable for both small- and large-scale operations.
Key Factors Driving the Future of Pyrolysis Oil Upgrading
Advancements in Technology: Ongoing research into new catalysts, more efficient hydroprocessing techniques, and advanced distillation methods will make it easier and more affordable to upgrade pyrolysis oil at a large scale.
Environmental Regulations: Increasingly stringent regulations around waste management and carbon emissions will push businesses to adopt more efficient and sustainable solutions, including upgrading pyrolysis oil for cleaner fuel production.
Economic Incentives: Governments may provide incentives for companies involved in waste-to-energy projects, including funding for pyrolysis units and upgrading technologies, making it more attractive for businesses to invest in these solutions.
Conclusion
Upgrading pyrolysis oil represents a key innovation in the waste-to-energy sector, offering the potential to turn low-grade waste products into high-quality, environmentally friendly fuels. As the world continues to seek solutions for plastic waste and cleaner energy, the ability to refine pyrolysis oil into premium fuels will play a crucial role in reducing environmental impact while contributing to a circular economy. By investing in oil upgrading technologies, businesses and industries can turn waste into valuable resources, creating a sustainable future for energy production.
Thursday, May 29, 2025
The Role of Egg Tray Machine in the Circular Economy and Paper Waste Recycling
The egg tray machine serves as a critical link in the broader framework of the circular economy, converting post-consumer paper waste into functional, biodegradable packaging. By transforming discarded fiber into protective trays, this machinery not only mitigates landfill pressure but also supports closed-loop material cycles in industrial ecosystems. Its utility spans across agriculture, logistics, and retail—industries under increasing pressure to decarbonize and minimize single-use plastics.
Converting Waste into Value
At the core of the circular model lies the revalorization of discarded materials. The tray making machine operates by pulping waste paper—such as old newspapers, cartons, and office paper—and remolding it into uniform tray structures. This process eliminates the need for virgin pulp, reducing the demand for wood-based resources and decreasing associated emissions from forestry and primary pulping operations.
The wet forming process is engineered for high retention efficiency, ensuring minimal fiber loss. Integrated filtration systems allow for water reuse within the circuit, further reducing the environmental footprint. What results is a cost-effective packaging solution derived from a resource that would otherwise be incinerated or left to degrade.
Reinforcing Localized Recycling Loops
Egg tray machine supplier supports decentralized recycling infrastructure. Small- to mid-scale operations can deploy localized units to process municipal or industrial paper waste on-site, bypassing the energy-intensive logistics of central processing plants. This regional production model enhances resilience, particularly in regions with limited recycling infrastructure or import-restricted economies.
Additionally, these machines empower agricultural sectors to generate their own tray packaging, closing material loops within the same production region. This kind of symbiosis is emblematic of industrial ecology—where waste from one process becomes the feedstock for another.
Replacing Single-Use Plastics in Transit Packaging
The molded pulp trays produced by these machines are gaining traction as substitutes for polystyrene and plastic alternatives in transit packaging. Their shock-absorption properties and thermal stability make them viable for egg transport, but their utility extends to other delicate commodities such as glassware, fruit, and electronics.
Egg tray machine supplier facilitates the mass production of biodegradable alternatives that degrade harmlessly in composting systems or naturally in the environment. This supports the systemic shift away from persistent synthetic materials, which remain one of the largest contributors to marine and terrestrial pollution.
Lifecycle Extension through Recyclability
Molded pulp trays, once used, can be re-entered into the pulp molding cycle. When returned through organized take-back systems or collected in standard paper waste streams, they become raw input for subsequent production runs. The egg tray machine is thus not only a converter but a reintegrator, maintaining the utility of cellulose fiber across multiple lifecycles.
Further, the machinery’s design accommodates a range of mold configurations, enabling producers to adapt tray designs for secondary packaging needs—extending product utility and reducing the demand for alternative packaging materials.
Conclusion
In the architecture of the circular economy, the egg tray machine functions as both processor and enabler. It diverts paper waste from linear disposal pathways, reintegrates material into value-added packaging, and reduces the ecological impact of transit protection. With continued innovation and regional deployment, egg tray machine supplier stands to become an indispensable tool in sustainable material management.
Subscribe to:
Posts (Atom)
Global Market Trends in Pyrolysis Plant Investments
The global market for pyrolysis plants is expanding rapidly, driven by increasing demand for sustainable waste-to-energy technologies. Urban...
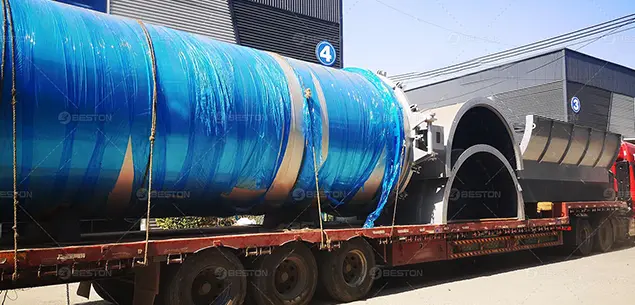
-
The automatic egg tray making machine plays a pivotal role in the production of egg cartons, enabling high-volume manufacturing with precis...
-
A tyre pyrolysis plant uses an industrial process that converts used tyres into liquid fuel, for example oils and gases. There are 2 varieti...
-
Producing charcoal can be carried out in several ways. Essentially, material which is combustible needs to be heated into a high temperatur...